CHEMICAL PROCESSING / CRITICAL FILTRATION APPLICATIONS
Fully Automatic | 1 Micron Filtration | Dry Solids Discharge (80% - 95%) | Cake Wash & CIP Options
The Oberlin Pressure Filter is a fully automatic filter that operates at up to 40-psi differential pressure to remove solids from liquids. The result is filtrate quality down to 1 mg/L at 1 micron and dry solids discharge at up to 95%. The Oberlin Filter is extremely versatile and is able to handle both extremes of the filtration spectrum.
- High solids (1% – 20% for many applications) – If it can be pumped, it most likely can be handled by an Oberlin Filter
- Low solids polishing – Filtration down to 1 micron. The Oberlin Filter can function as an automatic 1-micron cartridge filter.
Replace older, problematic equipment with an Oberlin Filter to recover/re-use your process liquid, or recover/reclaim your process solids.
THE OBERLIN PRESSURE FILTER ALTERNATIVE
Used in place of other liquid solid separation technologies.
OLD TECHNOLOGY
NEW TECHNOLOGY
Cartridges / Bag Filters
- Automatic Media Change Out
- Reduce or Eliminate Media Costs Using Rolled Media or Cleanable Belt
Filter Press
- Horizontal Surface Provides a Stable Cake Formation
- Easier for Dilute Slurry Handling
- Suitable for Batch Processing
- Uniform Cake Washes
- No Downtime for Operator Cleaning and Setup
- Minimal Human Exposure
- No Hydraulic Packages
Verti-Press & Tower Press
- Cuts Equipment Costs by Half
- Simplicity of Design Reduces Maintenance Downtime and Costs
Centrifuges
- Less Capital Cost
- Excellent Filtrate Quality
- High Solids Recovery
- No Special Foundation Needed
- No High Speed Rotating Parts for Lower Maintenance and Minimizing Crystal Product Damage
Rotary Vacuum
- No Vacuum Pump Means Less Energy Consumption
- Higher Pressure Differential for More Solids Capacity
- Minimizes or Eliminates Need for Filter Aids
- Minimal Product Exposure
Strainers
- Dry Solid Discharge – No Messy Backwashes
- Improved Solids Separation
Clarifiers
- One Step Separation to Dry Solids and Clean Liquid
Others
- Call Oberlin Filter to Compare
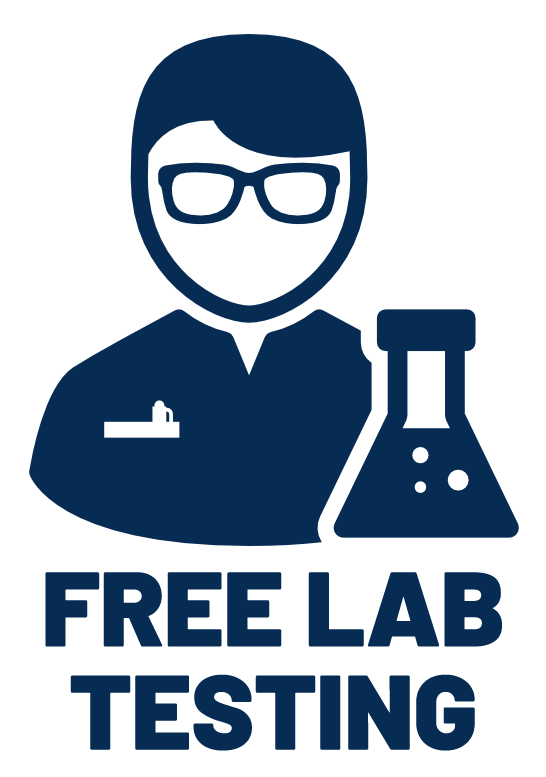
At Oberlin, we're dedicated to providing not just any solution, but the best one for you. Provide a sample of your contaminated process fluid to us. We'll come back with a test report, showing our ability to ensure the cleanest fluid and the highest return on investment for your operations.
OBERLIN PRESSURE FILTERS
Used in place of other liquid solid separation technologies.
Discover Oberlin's Versatile Filtration Solutions
The pneumatic actuator moves the filter chamber (platen) into position, and holds it against the other chamber. Platen seals on the perimeter of the chamber create a liquid-tight seal around the filter media (disposable or semi-permanent belt). Solids-bearing liquid is pumped into the upper chamber, where the solids are trapped by the filter media. Pump pressure continues to force the liquid through the filter media and the previously collected solids.
2. DRYING CYCLE
When the pressure inside the filtering chamber reaches 30-40 psi, compressed air or other inert gas is fed into the upper chamber. This forces the remaining liquid in the chamber through the trapped solids and filter media. After all the liquid is evacuated, the cake is further dried using the compressed air. Once the drying cycle is complete, determined by backpressure and elapsed time – the chamber is lifted.
3. DISCHARGE CYCLE
Once the chamber is lifted, the solids (filter cake) are automatically discharged by advancing the filter media one section. After discharge, the upper chamber descends and a new filtering cycle begins. This sequence continues automatically until ended manually or via electrical signal.
Technical Specifications
Not sure if the Oberlin Filter will meet the demands of your application? Start by comparing the Oberlin Filter design and features to your requirements. Finish by contacting our technical sales staff.
Mechanical
Materials of Construction
- Standard – Carbon Steel, 304 SS
- Options – 316 SS, 2205 Duplex SS, High Nickel Alloys, Any Other Weldable Material
Surface Finishes
- Standard – Mill Finish
- Options – Bead Blasted and/or Polished
Coatings
- Standard – Direct to Metal Paint, 2 Step Prime or Paint with High Build Epoxy or Urethane at 5 Mils
- Options – Polyarmor Plastic Flame Coating
Hose and Seal Materials
- Standard – Buna N, EPDM, Viton
- Options – Silicone, Teflon, Peek
Electrical Control
- Standard – Local PLC & HMI
- Options – Remote PLC & HMI, Remote I/O, Networked with Customer Controls
Electrical Design
- Standard -NFPA 79 – Electrical Standard for Industrial Machinery
- Options – UL, CSA, CE, Classified Areas
Utilities
Voltage
- Standard – 380-480V, 3Ph, 50/60 Hz,
- Options – 100-120V, 1Ph, 50/60 Hz
Pneumatic
- Standard – 80-110 PSI Plant Air,
- Options – 60 PSI Plant Air, Nitrogen, Others
Oberlin Filter Features
High Differential Pressure (Up to 40 PSI) -Cleaner Filtrate
- More, and Tighter Filter Media Options – Cleaner Filtrate
- Longer Filtering Cycles, Thicker Cakes – Cleaner Filtrate
- Maximizes Fluid Value (If Fluid is Product)
Dry Solids Discharge (Up to 98%)
- Minimizes Disposal Costs (if Solids are Waste)
- Maximizes Solids Value (If Solid is Product)
- Maximizes Solids Value (If Solid is Product)
Fully Automatic
- Two (2) Button Start/Stop
- Minimal Operator Intervention to Change Disposable Media Feed and Takeup Rolls
- Minimizes Contact with Hazardous Materials
Simple & Elegant Design
- Only Two (2) Moving Parts (Filter Chamber & Media Drive Motor)
- No Precise Guide Mechanisms to Bind, Replace
- Self-Adjusting Sealing Mechanism
- True 4-Sided Sealing, Absolutely No Bypass Around Seals into Clean Filtrate
- Full Containment for Pinch and Spray Protection
Options
Clean In Place (CIP)
- Maximizes Uptime
- Minimizes Contact with Hazardous Materials
Cake Wash
- Enhance Purity of the Filter Cake, and/or Reclaim the Maximum amount of Process Liquid
Outlet Recirculation
- Return Initial Filtrate to the Front of The Process
Bleedoff Function
- Contents Inside the Filtering Chamber can be Purged to Maximize Filter Capacity, and/or to Abort a Filtering Cycle
Semi-Permanent Belts
- Semi-Permanent Belts for Some Applications
Filter Aid Pre-Coat / BodyFeed Systems
- Efficient Use of Filter Aid (If Preferred or Required for the Application)
Fume Hood
- Capture Vapors from the Filter and Solids Hopper for Evacuation, and/or Scrubbing